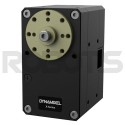
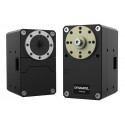
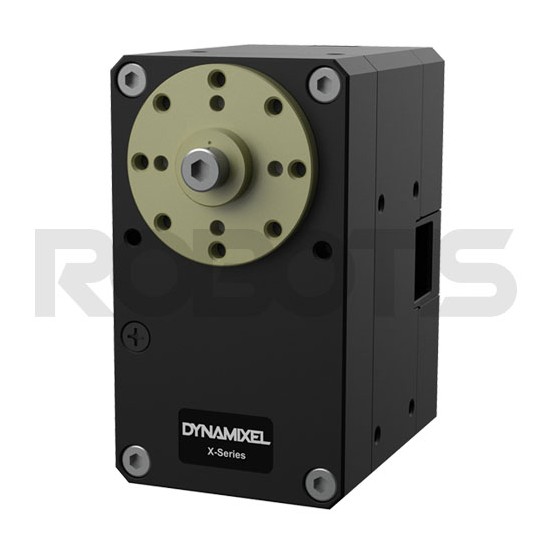
Get a quote in only 3 steps!
1. Add the items you are interested in to your cart
2.Go to your cart
3.Click on GENERATE A QUOTE
Tous vos devis sont accessibles à partir de votre compte client.
Including €0.05 for ecotax
Offering lots of torque and numerous control modes, the Dynamixel XM540-W270-Tservo motor with a TTL interface is a great choice for your all-terrain mobile robots and your most powerful creations.
The XM540-W270-T servo motor stands out from the Dynamixel X-series models for its very powerful stall torque of 10.6 Nm (though it only weighs 165 g). This is particularly interesting for all your robotics projects designed for carrying heavy payloads or exploring difficult terrain.
As compact as the other models in the series (less than 6 cm high and just 3.35 cm wide), it features a TTL connection, is very energy efficient, and includes an improved case offering better heat sink. Benefiting from a high-quality motor and the right choice of materials, this servo is as reliable as it is durable.
Robotis has developed a whole range of fully programmable servos that you can control in every aspect. PWM, position, consumption, temperature, speed... This servo provides extensive feedback, as always. Six control modes are available: torque, position, velocity, extended position, current-based position and PWM. It also includes a PID controller, a popular regulator used in industrial applications.
In short, you’ll have a servo ready in all circumstances, from prototyping to competition robots to autonomous navigation or robotised arms. The Dynamixel XM540-W270-T servo motor adapts just as well to use in a classroom environment as in a research lab, or for developing automated process solutions.
We’ve gathered below everything you’ll need to make the most of your Dynamixel XM540-W270-T servo motor:
Check that your Dynamixel servomotor is correctly configured. Do not hesitate to re-flash it with the ROBOTIS Software Roboplus. After re-flash remember to re-configure it. If the issue is not solved, contact us for an advanced support.
The motor is probably not well mounted. Check that you correctly mounted the horns by respecting the mark.
There is probably a mechanical issue with the Dynamixel servomotor. You can directly contact us to get more advance support.
Check your power supply and the system cabling (try with a different servomotor). You can also reset the servo. If nothing works, the best solution is to go through the Dynamixel servomotor checklist!
The 1.0 protocol is dedicated to the Dynamixel AX and MX series. Protocol 2.0 is for the X and Dynamixel Pro series. Protocol 2.0 control tables include PID controls which allow for more precise adjustment of the servo motor movements. Protocol 2.0 can be updated on MX series servo motors. You can refer to the protocol 1.0 and protocol 2.0 pages for more informations.